Lithoverde®
03.2022
“Suddenly, having put it all together, I realised how beautiful it was,” says CEO Gabriele Salvatori“
Innovation can come from unlikely places, including – as is the case for the world’s first recycled stone surface – the landfill
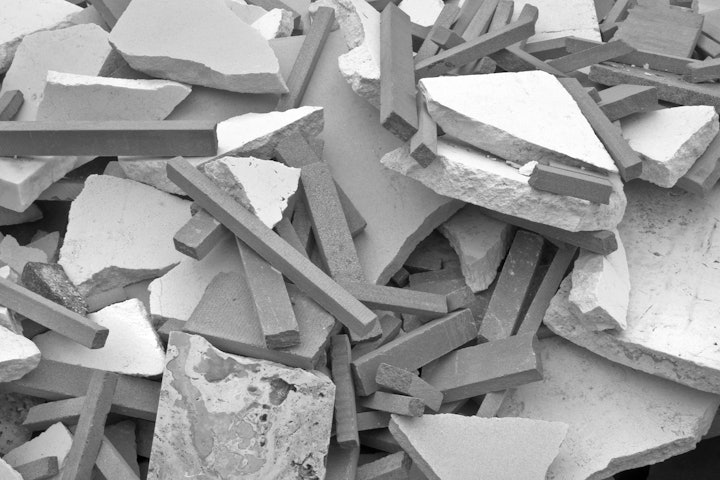
Where once great towers of off-cuts and broken slabs would pile up outside our factory in Northern Tuscany, waiting to be taken to landfill by specialist contractors, today little is thrown away. It’s no small feat in an industry where normally, by the time you arrive at a finished product, less than half the original block of stone is being used, and it is all down to one, particularly innovative, new product.
We started to investigate how we could use our excess stone in 2004. Cutting away chips or imperfections, the discarded tiles were arranged on a vast tray, fitting together like a puzzle to create a unique arrangement of different sized strips. “Suddenly, having put it all together, I realised how beautiful it was,” says CEO Gabriele Salvatori. “
I realised that if we could bond together these individual pieces and make a new slab, we could cut sections to create new surfaces.”
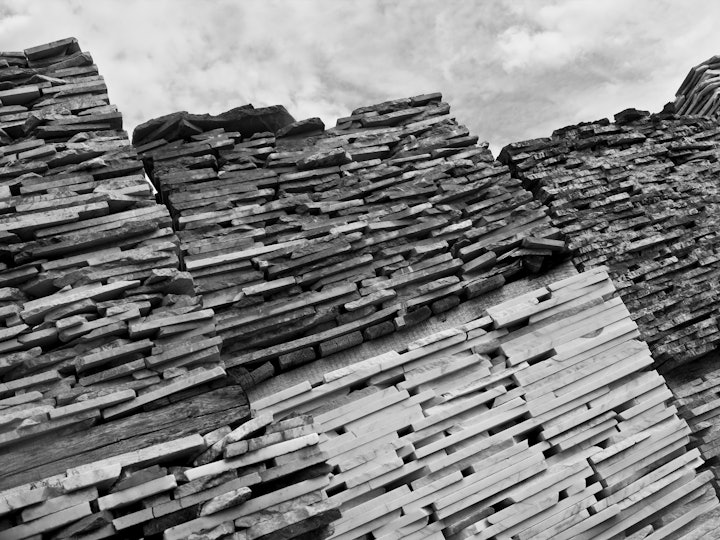
It was a big ‘if’, however, and industrialising the process would test the capabilities of our research and development department. To speed up production, it was decided that one layer of reclaimed tile would be covered with another, like a drywall, to form a new block – the idea being that these could be glued together in one process. It took some experimentation but eventually it was found that the block could be inserted into an autoclave, where the air is sucked out to create a vacuum, and a soy-based resin injected to fill the gaps between the stone. It’s a simple but innovative, high-tech solution, and one that no other company would have the equipment or technical understanding to achieve.
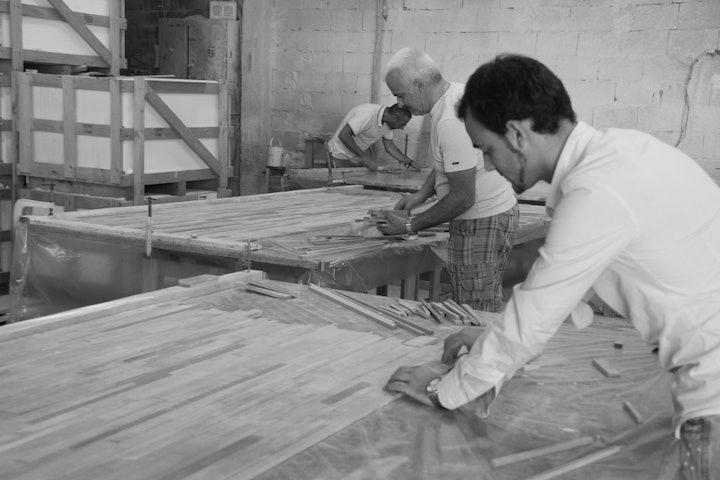
The result is a product that consists of 99% recycled materials – the extra 1% being the natural resin – and the only stone to be recognised by the US Green Building Council, meaning it contributes to a building’s overall environmental rating. Named Lithoverde® – a combination of the Greek word for ‘stone’ and the Italian word for ‘green’ – the product was so well-received that we quickly ran out of waste, a challenge that was met by acquiring more discarded stone from other companies nearby, further reducing the amount of waste that went to landfill.
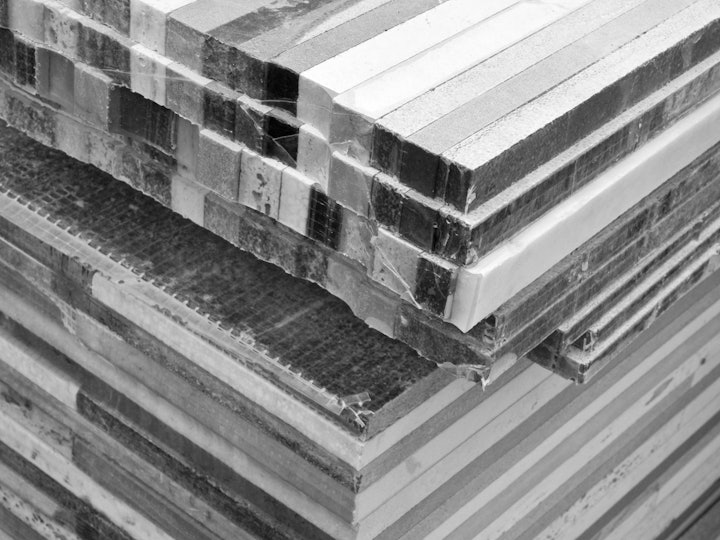
“Lithoverde® proves that it is possible to produce something that really adds value,” says Gabriele. “Both from an aesthetic perspective and an environmental one.” And more than establishing a benchmark of environmental responsibility in the industry, Lithoverde® has had a great impact within our company. Believing that companies have an important role to play in reducing the strain on our planet, in minimising the effects of global warming, we have worked to reduce the styrofoam in our packaging and we are now researching natural fibres that can be used to protect the stone in transit. “In the future,” adds Gabriele, “all new products will have to do better than what we have done before from an environmental standpoint.”
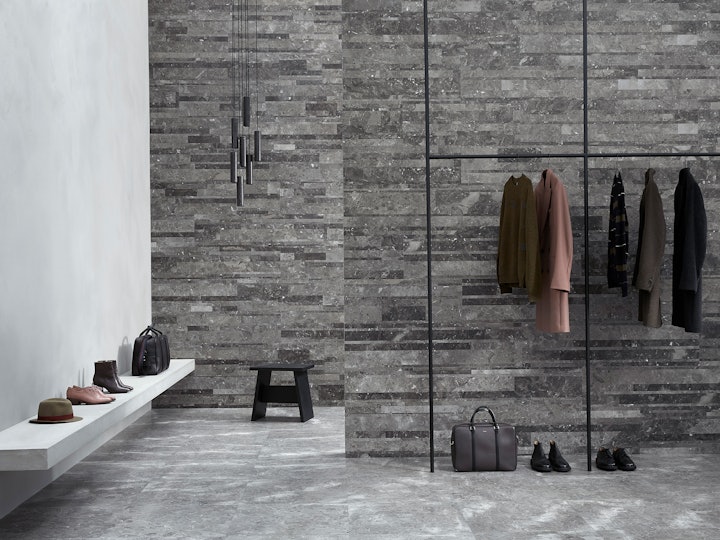
Stone is an inherently environmentally conscious product. Ancient structures built thousands of years ago from stone are still standing – a durability no other architectural material can offer – but the way stone has been used in the modern era is not sustainable. In celebrating the unique qualities of every piece of stone, the variations in colour and pattern, Lithoverde® is the only product to truly harness the environmental potential of stone.